Monitor Your Conveyor System Optimally and Set Alerts in Banner CDS
Identify and Correct the Source of Reduced Output in One or Multiple Production Lines with Snap Signal
A bottling operation has four steps in its process: filling, capping, labeling, and packaging. One of the plant’s production lines routinely underperformed; it frequently had lower output than the other lines. The production manager wanted to identify the step that created bottling constraints and quantify losses caused by the underperforming line. Troubleshooting this issue would determine how to increase output on the other lines. The bottling machine in question was older and had no way to monitor throughput.
Snap Signal products utilized existing legacy sensors that were already installed to offer valuable insights on process states and error conditions. Product managers were able to monitor machine performance and help optimize throughput via sensor data sent to Banner Cloud Data Services (CDS). Performance metrics were used to identify system bottlenecks, make personnel scheduling decisions, and determine which line upgrades offer the best ROI.
Model and Description:
- DXMR90-X1 - Industrial Controller with edge processing and cloud capability
- QS18K6AF120Q8 - Photoelectric Proximity Sensor with Discrete Output
- S15C-B22-MQ - Snap Signal converter that converts Discrete (PNP or NPN) signals into Modbus
- CSB-M1250M1250-T - Tee connector
- CSB-M1248M1241 - Parallel Wired M12 Splitter
- MQDC-4506SS - M12 Extension Cordset
- STP-M12D-406 - 4-pin M12 D-code to RJ45 Shielded Ethernet Cordset
Lengths for cordsets and splitters listed are examples. Please consult the Banner Engineering website or reach out to an Application Engineer for the correct lengths.
Featured Products
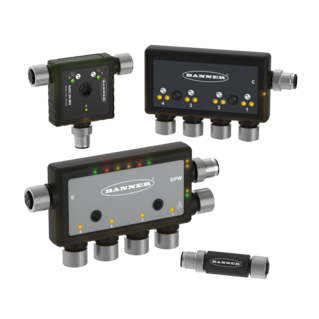
- Technologies
- Asset Monitoring Gateway with Cloud ID
- Asset Monitoring Gateway with SNAP ID
- Codesys
- Condition Monitoring
- Ethernet in Hazardous Locations
- Field Logic Controller
- Industrial Cloud
- Industry 4.0
- IO-Link
- Machine Safety
- Modular Machines
- Module Type Package
- Multiprotocol Ethernet
- Pick-to-Light
- Profinet
- RFID
- Snap Signal
- Sustainability
- TAS – IIoT Service Platform
- The Visual Factory